Publicado: August 2nd 2016

Uno de los fabricantes más antiguo y respetado de combustibles sintéticos, lubricantes y productos químicos de Sudáfrica está especificando marcos de rodillo de alto rendimiento y sellos de faldón en sus transportadores de carbón para ayudar a la compañía a prevenir derrames y evitar que las partículas pequeñas se escapen del flujo de material. Los nuevos componentes de Martin Engineering South Africa están demostrando ser eficaces en la contención del material fugitivo, la minimización de los riesgos para la seguridad y la pérdida del tiempo de producción, y en la reducción significativa del tiempo de mantenimiento y el uso de agua de lavado.
Sasol Synfuels se fundó en 1950 para comercializar la tecnología de carbón a líquidos en Sudáfrica, y se ha transformado en una compañía internacional de energía y química con más de 34 000 empleados en 38 países diferentes. La compañía que desarrolla y comercializa nuevos procesos y tecnologías y construye y opera plantas para producir una variedad de flujos de productos como combustibles líquidos, productos químicos y electricidad.
La planta de procesamiento de carbón del oeste en Secunda produce una suspensión de carbón húmedo que se prensa para formar tortas de combustible, que descienden por un conducto de 5 metros. Con una velocidad de banda de alrededor de 3.6 metros por segundo, la operación procesa aproximadamente 1.6 millones de toneladas por mes.. El gran volumen de material y la relativamente alta velocidad tendían a generar pequeños derrames, que con el tiempo formaban acumulaciones significativas, lo cual exigía a los trabajadores de mantenimiento retirar los potenciales peligros para la seguridad y lavar el material en un sistema de contención especialmente diseñado.
“El efecto de ese material fugitivo era la necesidad de usar mano de obra que tenía que ser separada de actividades importantes para eliminar las acumulaciones todos los días”, explicó Koos Meyer, gerente de división de las plantas oriental y occidental. "Requería una gran cantidad de agua y nos dejaba con una cantidad significativa de residuos que debían tratarse. Estamos buscando una manera de evitar que los derrames escaparan de la corriente de proceso en primer lugar, para evitar el material perdido y dedicar el personal a una actividad que generara ganancias."
Los representantes de Martin Engineering inspeccionaron las cinco bandas que tenían entre 12 y 20 metros y revisaron las áreas problemáticas con el personal de Meyer. "Descubrimos una pérdida de estabilidad en la trayectoria de la banda cuando pasaba sobre ciertos rodillos", observó el representante de Ventas Técnicas Ronald Wilmot. "Este movimiento indeseado estaba alterando el material lo suficiente como para liberar pequeñas cantidades por vez en el flujo. Como estas bandas no tenían sello de fald´ón, el derrame resultante no tenía contención".
Durante la primera etapa de la actualización del transportador, los técnicos de Martin instalaron un total de 138 bastidores de rodillos Trac-MountTM en tres estructuras de bandas de 900 mm de ancho. “A pesar de que la banda tenía originalmente 900 mm, fabricamos un bastidor de rodillo Trac-MountTM de 1,050 mm que se adaptara a la banda de 1,050 mm debido al aumento en la producción”, dijo Wilmot.
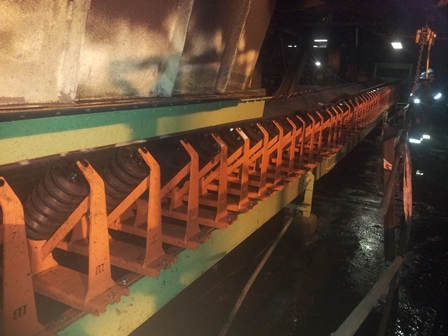
Estas unidades modulares tienen un innovador diseño que le permite cargar en los espacios estrechos que hay entre las camas de soporte y permiten un correcto transporte de la banda para estabilizar la carga y mejorar el sellado. Además pueden ser reparadas por un solo trabajador sin necesidad de elevar la banda ni mover los rodillos adyacentes. Los ensamblajes fueron fabricados con un bastidor deslizante sobre una base fija y pueden entregarse con rodillos de impacto o acero de la clase A, B, C, D o E de CEMA.
Los bastidores estándar necesitan solo ocho pulgadas (203 mm) de espacio para rodillos de 6 pulgadas (152 mm). Martin Engineering puede diseñar también rodillos especiales para satisfacer requerimientos únicos. Disponemos de opciones que son totalmente de acero, con ángulos de bastidor ajustable y la capacidad de funcionar con diseños de rodillo alternativos.
Una vez solucionado el origen del problema de los derrames mediante la estabilización de la banda, los técnicos también instalaron 42 metros de faldón de poliuretano para brindar un sello adicional contra el polvo. “Suministramos grandes cantidades de este faldón a Sasol, principalmente debido a su durabilidad y flexibilidad”, agregó Wilmot. “Esto funciona muy bien en estas aplicaciones”.
Desde que se completaron esta mejora, los resultados fueron excelentes y el personal de Sasol ha informado que prácticamente no ha habido derrames en las secciones renovadas. Las limpiezas disminuyeron proporcionalmente en el área. “Estamos muy felices con la renovación”, concluyó Mayer. “El equipo funciona muy bien y la instalación fue muy ordenada y profesional”. Se han programado mejoras similares para las dos bandas finales y esas tareas ya han comenzado. Además, los técnicos de Martin Engineering han comenzado a trabajar en un proyecto que es prácticamente idéntico en la planta de procesamiento de carbón del este de Sasol.