Publicado: August 2nd 2016
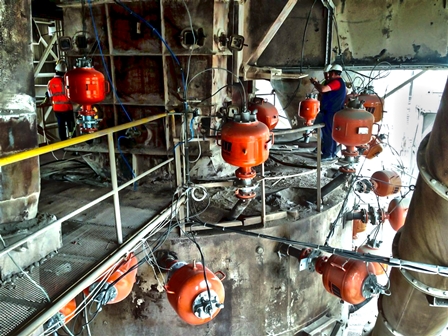
La planta de cemento Büyükçekmece ubicada en el oeste de Estambul, en Turquía, con una capacidad de producción de 5900 toneladas de clinker por día. La planta está operada por el Akçansa Group (una empresa conjunta entre Turkish Sabanci Holding y German Heidelberg Cement) y es uno de los principales productores de la ajetreada industria del cemento de Turquía, que suministra un 10 % de la demanda total del país y un 12,5 % de las exportaciones nacionales totales de cemento y clinker. Las instalaciones se construyeron originalmente en 1967 y cuentan con tres hornos de producción de clinker que suministran cemento principalmente a la región de Marmara en Estambul.
Literalmente pionera en el uso de combustible alternativo en la industria del cemento de Turquía, la planta recibió la primera licencia para su proceso en 2005, el mismo año en que instaló un alimentador de neumáticos especial construido por ella misma. La proporción actual de combustible es aproximadamente del 77 % de coque de petróleo y del 23 % de combustibles alternativos, incluido aceite de desecho, combustibles derivados de residuos (RDF), neumáticos, plásticos industriales y lodo seco de depuradoras.
El problema de la acumulación
A medida que la capacidad de la planta aumentaba y cambiaban los tipos de combustibles con los años, los trabajadores comenzaron a tener que retirar manualmente la acumulación de material en la torre de precalentamiento Cyclone 4 del horno N.° 2 para poder mantener la producción. Los cierres imprevistos para permitir la limpieza del ciclón y del tubo profundo interferían con los cronogramas de producción y exponían al personal de mantenimiento a potenciales riesgos.
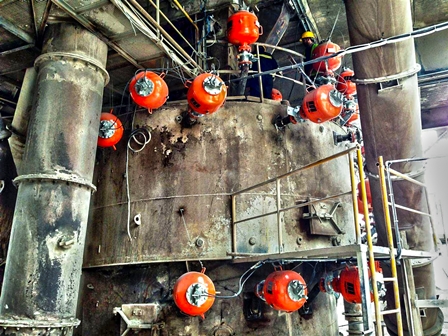
Estas acumulaciones pueden ser especialmente graves cuando se utilizan combustibles con alto contenido de sulfuro o cloruro como coque de petróleo y combustible derivado de residuos. En casos extremos, las acumulaciones masivas pueden desprenderse inesperadamente y ahogar el proceso, además de causar importantes daños en el equipo.
Además del tiempo de enfriamiento necesario, el proceso de limpieza ciclónico requiere que 3 o 4 personas trabajen con martillos neumáticos a través de las puertas de acceso y durante varias horas, combatiendo con el calor y el polvo. Fue necesario utilizar más energía para reiniciar el proceso y volverlo a llevar a la temperatura operativa. Lamentablemente, aun después de invertir todo ese tiempo y energía, la acumulación era tan grave que el problema volvía a repetirse a la semana, ahogando el flujo del material y forzando otro cierre. Los ejecutivos de la planta se pusieron en contacto con Martin Engineering Turkey para realizar una auditoría del proceso y se desarrolló un esfuerzo conjunto para determinar cuál era la solución óptima.
Un método comprobado
Una vez finalizada la auditoría, se determinó que la mejor opción para que el sistema regresara al flujo normal y evitar los bloqueos en el futuro sería una serie de cañones de aire. La tecnología del cañón de aire tiene una larga historia de servicio en el procesamiento del cemento, ayudando a mejorar el flujo del material y a reducir la acumulación. La descarga programada de un chorro de aire dirigido puede prevenir la acumulación que afecta la eficiencia del proceso y aumenta los gastos de mantenimiento, ayudando a los fabricantes a minimizar la necesidad de interrupciones en el proceso y mano de obra manual.
Los dos componentes básicos de un cañón de aire son una válvula de acción rápida y alto flujo y un recipiente de presión (tanque). El dispositivo realiza el trabajo cuando el aire comprimido del tanque es liberado repentinamente por la válvula y dirigido a través de la tobera, la cual está estratégicamente posicionada en la torre, el conducto, el ciclón o en otra ubicación. La red de cañones de aire se instala frecuentemente en una serie y se secuencia con precisión para obtener el máximo efecto, puede ser programada para adaptarse mejor a las condiciones individuales del proceso o a las características del material.
La descarga de aire descompone las acumulaciones de material y libera los recorridos bloqueados, permitiendo que los sólidos y los gases reanuden el flujo normal. Para personalizar la instalación del cañón de aire y adaptarlo al entorno de servicio, se pueden obtener características específicas de chorro de aire mediante la manipulación de la presión operativa, el volumen del tanque, el diseño de la válvula y la forma de la tobera.
Los ingenieros de las dos compañías se reunieron para hablar sobre los detalles como el diseño del cañón de aire, la selección de la tobera y las ubicaciones específicas para mantener un flujo óptimo del material. Para controlar las acumulaciones de material y mantener la estabilidad de la producción, se instalaron 29 cañones de aire Martin® Hurricane suministrados por Martin Engineering Turkey cada uno, con un depósito de 70 litros instalados en ubicaciones estratégicas por un equipo de servicio MartinPLUS®.
La instalación incluyó toberas turbofán de alta velocidad con blindajes de protección térmica Martin®para proteger al personal de mantenimiento cuando inspeccionan o reparan el sistema del cañón de aire. Los blindajes de protección térmica Martin® se conocen también con el nombre de protección contra ráfaga y se encuentran entre el proceso y la válvula misma del cañón de aire. Estos dispositivos están disponibles en modelos que pueden ser operados en forma neumática o manual y ayudan a prevenir el reflujo de material durante las reparaciones además de proteger los componentes de la válvula del cañón de aire contra el rociado del material.
Los nuevos cañones de ahí que fueron distribuidos en tres grupos y cada uno era dirigido por la sala de control de la planta. La secuencia de descarga se desplazaba hacia arriba en espiral, con cañones que disparaban con secuencias de 10 segundos de intervalo. Todo el ciclo de 80 a 90 segundos se repite generalmente aproximadamente cada 20 minutos, pero los operadores han variado el tiempo de cinco a 45 minutos, dependiendo de las condiciones operativas particulares.
Desde la instalación de la nueva red de cañones de aire, no se registraron cierres no programados que hubieran sido causados por la acumulación de material en la sección del ciclón. Una vez resuelto el problema, de los ingenieros dirigieron su atención a otras acumulaciones que estaban más arriba, en el tubo profundo, un área que no era cubierta por la red de los cañones de aire. Durante el próximo cierre, la planta instalará un conjunto adicional de cuatro cañones de aire Martin® 70L Hurricane que se colocarán arriba del tubo profundo del ciclón.
Reducción de costos
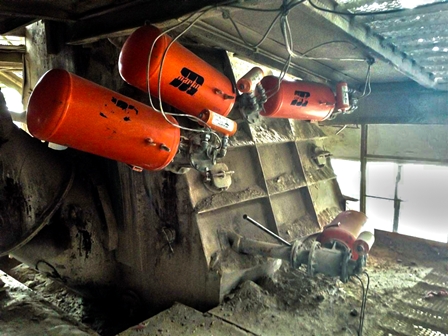
La auditoría reveló también la oportunidad de reducir los costos operativos de los 22 cañones de aire Martin® Tornado de la instalación en la cámara de entrada y en el ducto elevador de la torre del precalentador del horno N.° 2 mejorando cada uno con un pistón de depósito de retorno Martin®, un recipiente que cierra la válvula una vez que se ha descargado aproximadamente el 50 % del volumen. El depósito es un dispositivo neumático que recoge el aire de salida de la válvula y redirige esa presión para cerrar el pistón cuando la válvula y la presión del tanque se nivelan.
Con el cañón de ahí que esta equipado con un depósito de retorno del pistón, produce una fuerza de disparo inicial de la misma potencia pero la duración de la descarga es menor. En vez, el aire retenido dentro del tanque del cañón minimiza el consumo de aire general sin reducir la fuerza de salida inicial. Como el tanque de aire principal nunca es completamente evacuado, el volumen de aire requerido para rellenar después de cada descarga es menor. Como la fuerza pico del cañón de aire no es afectada, se puede realizar la misma cantidad de trabajo con la mitad del aire comprimido.
Antes de la instalación de los depósitos de retorno, se calculaba que el consumo de aire de 22 cañones de aire Martin® Tornado en Büyükçekmece era de 2 metros cúbicos por minuto lo cual equivalía a un consumo total de aire anual de aproximadamente 525,600 metros cúbicos. Si se estima que el costo del aire de servicio es de 2 centavos por metro cúbico, el costo total del aire sería de $10,512 por año. Después de la instalación de los depósitos, el consumo anual de aire se redujo a 262,800 metros cúbicos y se mantuvo el mismo rendimiento del cañón de aire. Si se estima que la vida útil mínima de un cañón de aire es de 10 años (lo cual, no es una perspectiva irrazonable), los ahorros en el costo durante ese período serían de$52,560.